Understanding the Essentials and Applications of Plastic Extrusion in Modern Manufacturing
In the realm of modern-day manufacturing, the method of plastic extrusion plays an instrumental function - plastic extrusion. This elaborate procedure, entailing the melting and shaping of plastic via specialized passes away, is leveraged across various industries for the creation of diverse products. From automobile parts to durable goods product packaging, the applications are substantial, and the capacity for sustainability is similarly outstanding. Untangling the fundamentals of this procedure exposes real convenience and potential of plastic extrusion.
The Basics of Plastic Extrusion Refine
While it may appear complex, the principles of the plastic extrusion process are based on relatively uncomplicated concepts. It is a manufacturing procedure wherein plastic is melted and after that shaped right into a continual account through a die. The plastic extrusion procedure is extensively used in numerous industries due to its cost-effectiveness, versatility, and performance.
Various Sorts Of Plastic Extrusion Techniques
Structure upon the standard understanding of the plastic extrusion process, it is needed to explore the different strategies involved in this manufacturing method. The 2 main strategies are profile extrusion and sheet extrusion. In profile extrusion, plastic is melted and developed right into a continuous profile, commonly utilized to develop pipes, poles, rails, and home window frames. In contrast, sheet extrusion creates large, flat sheets of plastic, which are normally more processed into products such as food packaging, shower curtains, and automobile components. Each method requires specialized machinery and exact control over temperature and pressure to guarantee the plastic preserves its shape during air conditioning. Understanding these techniques is essential to using plastic extrusion successfully in modern-day production.
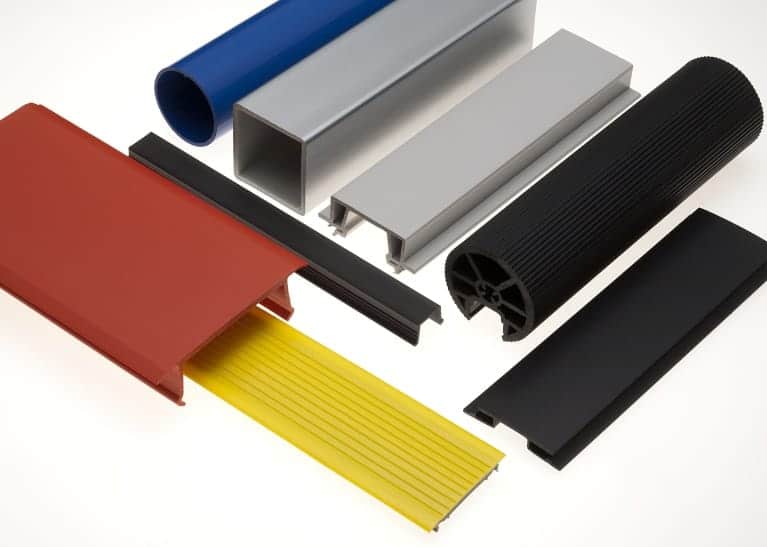
The Duty of Plastic Extrusion in the Automotive Market
A frustrating bulk of parts in modern-day lorries are items of the plastic extrusion process. Plastic extrusion is largely made use of in the manufacturing of different auto components such as bumpers, grills, door panels, and dashboard trim. Hence, plastic extrusion plays a pivotal role in automobile production.
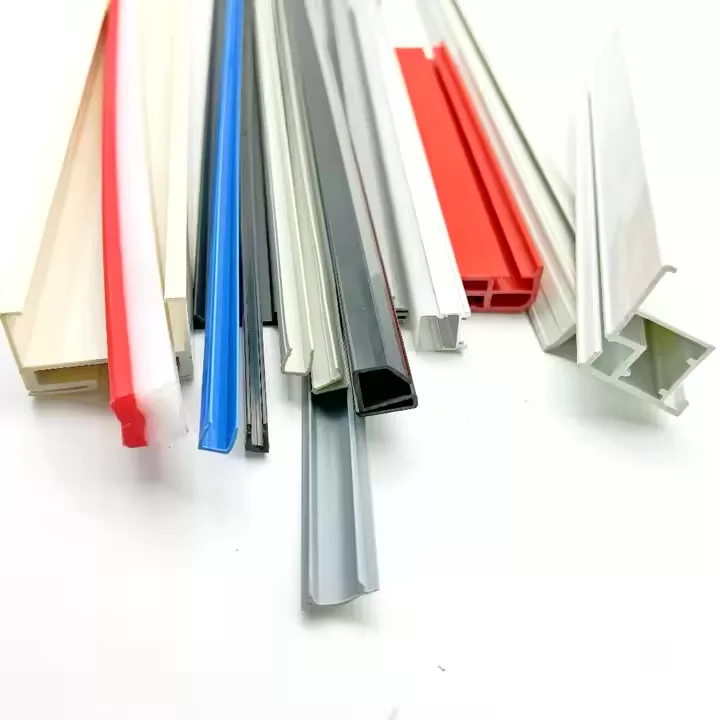
Applications of Plastic Extrusion in Consumer Item Production
Past its considerable influence on the automotive industry, plastic extrusion verifies just as effective in the world of consumer products making. The adaptability of plastic extrusion permits producers to create and generate complex forms and sizes with high precision and performance. The flexibility, versatility, and cost-effectiveness of plastic extrusion make it a recommended selection for many consumer products producers, adding significantly to the industry's development and advancement.
Ecological Impact and Sustainability in Plastic Extrusion
The pervasive over here use plastic extrusion in producing welcomes scrutiny of its ecological effects. As a process that frequently uses non-biodegradable products, the environmental impact can be significant. Power intake, waste manufacturing, and carbon exhausts are all concerns. Market developments are enhancing sustainability. Effective equipment decreases energy use, while waste monitoring systems reuse scrap plastic, decreasing raw product needs. Furthermore, the advancement of naturally degradable plastics provides a much more eco-friendly choice. Regardless of these renovations, additionally technology is required to minimize the environmental footprint of plastic extrusion. As culture leans in the direction of sustainability, suppliers have to adapt to remain viable, stressing the value of constant research and advancement in this area.
Final thought
In final thought, plastic extrusion plays a crucial role in modern production, especially in the automotive and customer goods markets. Its flexibility permits the production of a vast range of components with high precision. Moreover, its capacity for reusing and development of eco-friendly materials provides an encouraging opportunity in the direction of sustainable techniques, thereby attending to ecological issues. Comprehending the essentials of this procedure is key to optimizing its applications like this and advantages.

The plastic extrusion procedure is extensively used in various markets due to its adaptability, cost-effectiveness, and efficiency.
Building upon the standard understanding of the plastic extrusion process, it is required to check out the different strategies involved in this production technique. plastic extrusion. In contrast, sheet extrusion creates big, level sheets of plastic, which are typically more refined Get More Information into products such as food packaging, shower drapes, and automobile parts.A frustrating majority of parts in modern cars are products of the plastic extrusion process